A refurbished jet engine will soon heat and cool a former meatpacking plant on Chicago’s South Side.
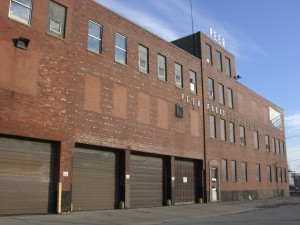
The Plant on Chicago's South Side is installing a combined heat and power system that will be powered with onsite waste by June 2013. Photo: Brian Bienkowski
The project is part of Chicago entrepreneur John Edel’s effort to turn a large vacant building into a vertical farm and home for sustainable small businesses. His optimistic plans for onsite energy are becoming reality.
The former jet engine will drive a combined heat and power system.
When electricity is produced there’s heat. Conventional plants don’t capture it. Think of smokestacks – a lot of what’s belched is lost heat.
Combined heat and power systems grab the heat, turn it into steam and put it to work. In this case that means making beer.
“We’ll be taking the steam and heat and piping it into the brewery, which will boil their kettles,” said Melanie Hoekstra, operations manager at The Plant, referring to New Chicago Beer Co., one of five tenants in the 93,500 square foot building.
After the heat boils brewery kettles, it will travel up to a chiller and the now-cold water will cool the building.
“We have many heat emitting processes here and very good insulation, so we’ll need the cold water to regulate the temperature,” Hoekstra said.
Most combined heat and power systems use natural gas, which is what The Plant will use for a while. But by June 2013, onsite waste will feed an anaerobic digester, creating methane for the engine, Hoekstra said.
The anaerobic digester is like a “mechanical stomach” that will be fed brewery and food waste, Hoekstra said. Bacteria break down the waste, just like in a human belly, and the result is about two-thirds methane and one-third carbon dioxide. The methane will power the jet engine.
Hoekstra estimates they will need about 10,000 pounds of waste each year, most coming from onsite.
The Plant has signed a contract with Alcor Energy Solutions out of Arizona. Alcor officials did not return calls for comment. But, according to the Center for Energy in Canada, jet engines are a good fit for combined heat and power systems since they are basically turbines that use methane or natural gas to rotate blades and generate electricity. Gas turbines tend to be used on large combined heat and power projects, according to the center.
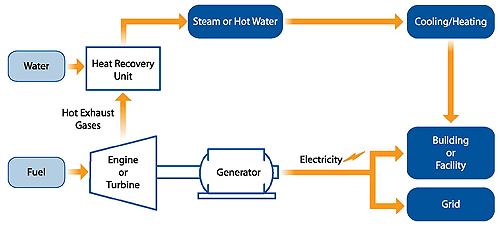
The flow in a combined heat and power system. Graphic: EPA
By using otherwise lost heat, the heat and power systems need less fuel and produce less greenhouse gases. They use up to 80 percent of fuels for power. Conventional plants use only 45 percent with the rest wasted, according to the U.S. Department of Energy.
If 20 percent of U.S. energy came from combined heat and power systems by 2030, the federal agency estimates that the carbon dioxide reduction would be like taking 154 million cars off the road.
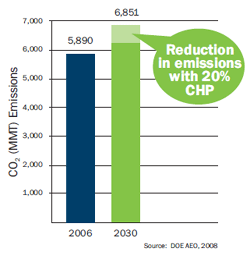
Expansion of combined heat and power systems would cut carbon dioxide emissions. Graphic: U.S. Department of Energy
The idea of capturing heat while generating power isn’t new. Many large industrial facilities have used these systems for years.
But, a seemingly intuitive switch remains hindered by status quo power and cost, said Anna Chittum, senior policy analyst at the American Council for an Energy Efficient Economy.
“This is an idea that’s not widely promoted by electrical utilities … it runs counter to their business model,” Chittum said. “When you put a combined heat and power system in, you reduce the amount of electric you buy from the grid, which is where they make their money.”
And the systems aren’t cheap. Cost depends on if it’s a new system or an addition to an existing one and what kind of fuel will be used.
The Plant received $1.5 million from the Illinois Department of Commerce and Economic Opportunity for the energy system. Total project costs are estimated at $3 million. The rest of the money will come from Bubbly Dynamics, another company owned by Edel that renovates and re-uses city buildings.
But there are long-term savings. A typical combined system costs about $.07 per kilowatt/hour, according to the EPA. The U.S. Bureau of Labor Statistics reports the national average for grid-purchased power was $.127 per kilowatt/hour in December 2011.
With a struggling economy many businesses shy from long-term investments.
“Seven-year paybacks are just too long for people that are just trying to keep the lights on,” Chittum said.
However, with fewer projects, manufacturers of combined systems have been cutting costs, Chittum said. Paybacks on more recent installations have been more like five years, she said.
The Department of Energy and the Environmental Protection Agency have been mostly supportive of combined heat and power projects, Chittum said. There are two federal tax incentive programs for the systems.
The Plant is looking long-term, Hoekstra said. The system is its way of leading by example when it comes to sustainability, she said.
“We’re showing that you can do high energy things and still do it in a renewable way,” she said. “This will really close the energy loop in the building.”